By Niko/Category: Equipment
Grease fittings or Zerk fittings were patented by Oscar U. Zerk in 1929, hence the name Zerk fittings. The assignee was the Alemite Manufacturing Corporation, and because of that often this type of fitting is ‘Alemite’ fitting. They’ve been used since the 1920s, and they’re far from obsolete. Ball check valves to accept grease under pressure from a grease gun already existed, but Zerk’s fitting was an improved style and less vulnerable to dirt. Grease fittings are metal fittings installed on mechanical systems to feed lubricants into a bearing under moderate to high pressure without overflow or leaks, by using a grease gun.
Put, grease fittings help you inject grease lubricant into wear points on different kinds of agriculture machinery including cars, trucks, motorbikes, plows, tractors, hay balers, industrial plant equipment, and others. It was introduced as an improved method of lubricating moving parts, and they come in various types including flush mount grease fittings, ball-joint, button head joint fittings, hydraulic couplers, safety fittings, and others. They can be manufactured using stainless steel, brass, and Monel materials.
This type of lubrication and bearing setup is simple, cost-effective, and long-lasting. Although the process of grease fittings may sound a bit complicated and unknown term, we’ll try to explain a bit more about it so it can help you better understand grease fittings.
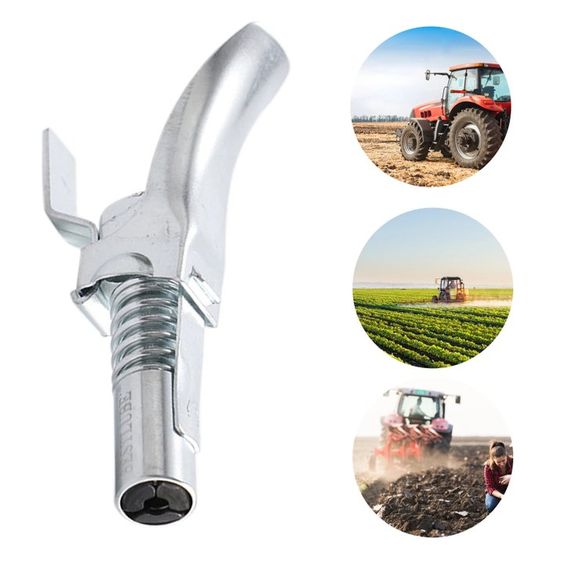
How Grease fittings work?
How often should you lubricate grease fittings?
Regular maintenance of your grease fittings is an integral part of machinery upkeep. It ensures the smooth operation of your equipment, reduces the chance of breakdown, extends the lifespan, and saves on expensive repair or replacement costs.
The recommended frequency of the grease fittings clean and fitting maintenance will vary based on the type and usage of the machinery, the environmental conditions, and manufacturer guidelines. Typically, a rule of thumb for most common equipment—be it in the industrial, automotive, or agricultural sector—is to check and service the grease fittings every 3 to 6 months.In the middle of the season, it is preferable to inspect and lubricate the equipment before and after each more intensive and long term work or agriculture operations.For example :ploughing, sowing preparation, combine harvesting,…
The potential consequences of failing to have broken fittings and keep up with recommended maintenance include inadequate lubrication, more friction, unnecessary wear and tear, overheating of components, and eventual machine failure. Regular monitoring and maintenance of your grease fittings will help you evade such preventable issues.
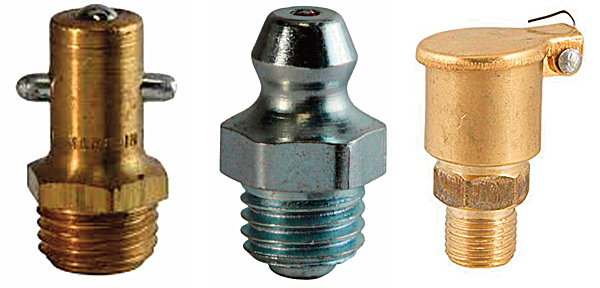
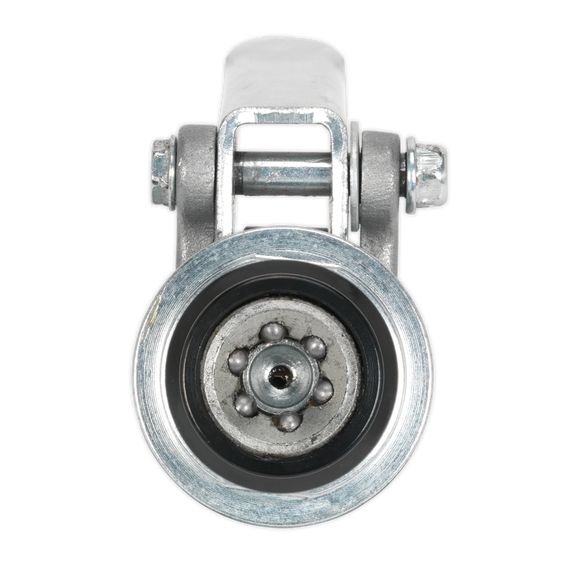
Safety tips for lubing a Grease fittings

1. Make sure that the fitting is clean before you attach the grease gun. You wouldn’t want to get dirt into the fitting.
2. Pump in the grease until you hear or feel increased resistance, and stop.
3. You should have a lubrication diagram for reference when you are servicing equipment that you’re not familiar with.
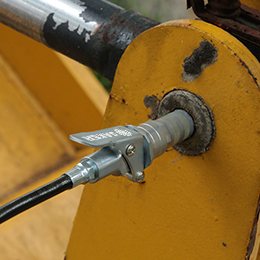
Are there different types of grease fittings?
Grease fittings come in a variety of types. Some of the most common include standard or grease Zerks fittings, button head fittings, flush type fittings, pin type and ball type fittings. Each drive-type grease fitting is designed for different applications or machinery and can come in different sizes and angles.
Grease fittings adapter
Grease fitting (zerk fitting) adapters are grease gun attachments and grease dispensing tips to help with both handheld applications and industrial dispensers. Sometimes you need an extension or to change from one thread to another or maybe a 45°/90° would make lubrication simpler.We discern e a range of fittings and adapters including:
- Grease fitting bushings – to convert thread sizes
- Zerk elbow adapters – 45, 65, 90 degree angles
- Pipe adapters – to connect grease-fitting pipes of all sizes
- Swivel adapters – grant mobility and flexibility without kinking the dispenser hose
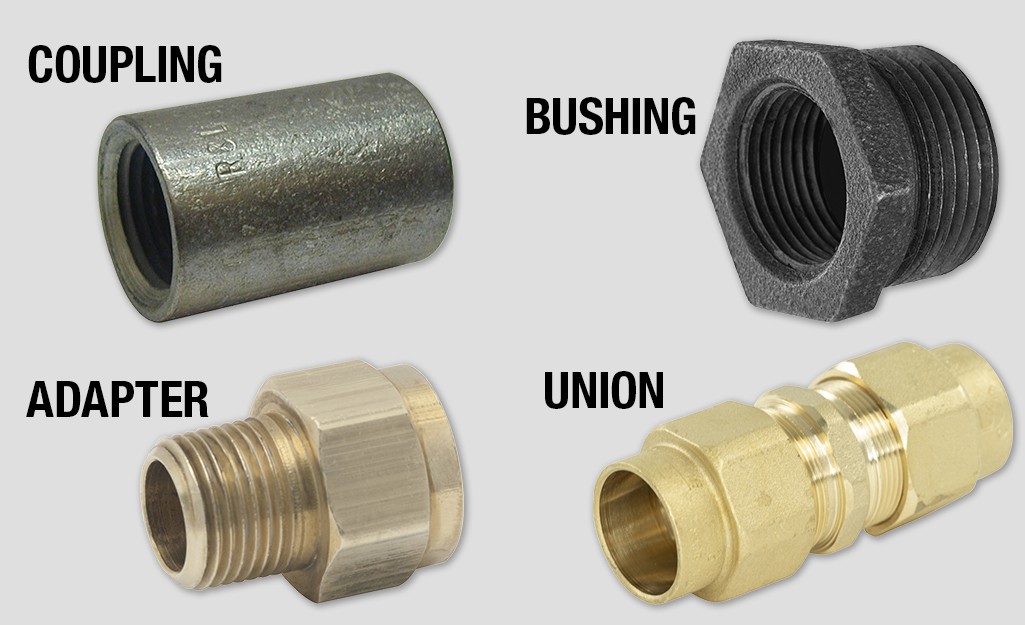
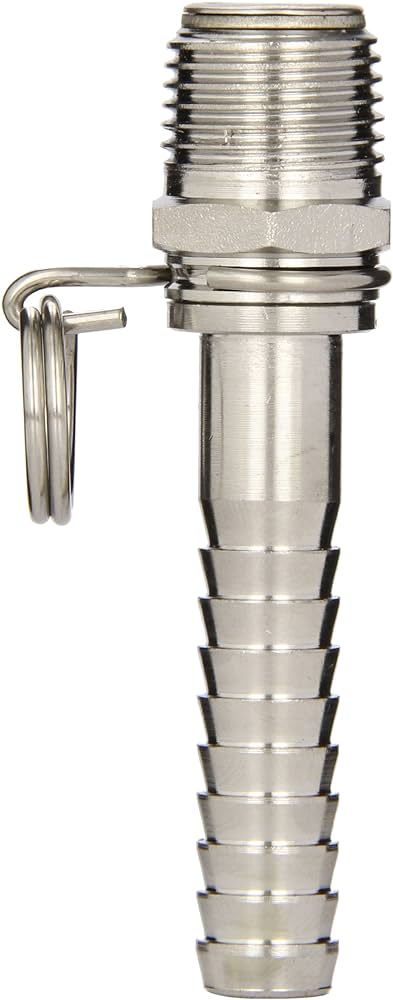
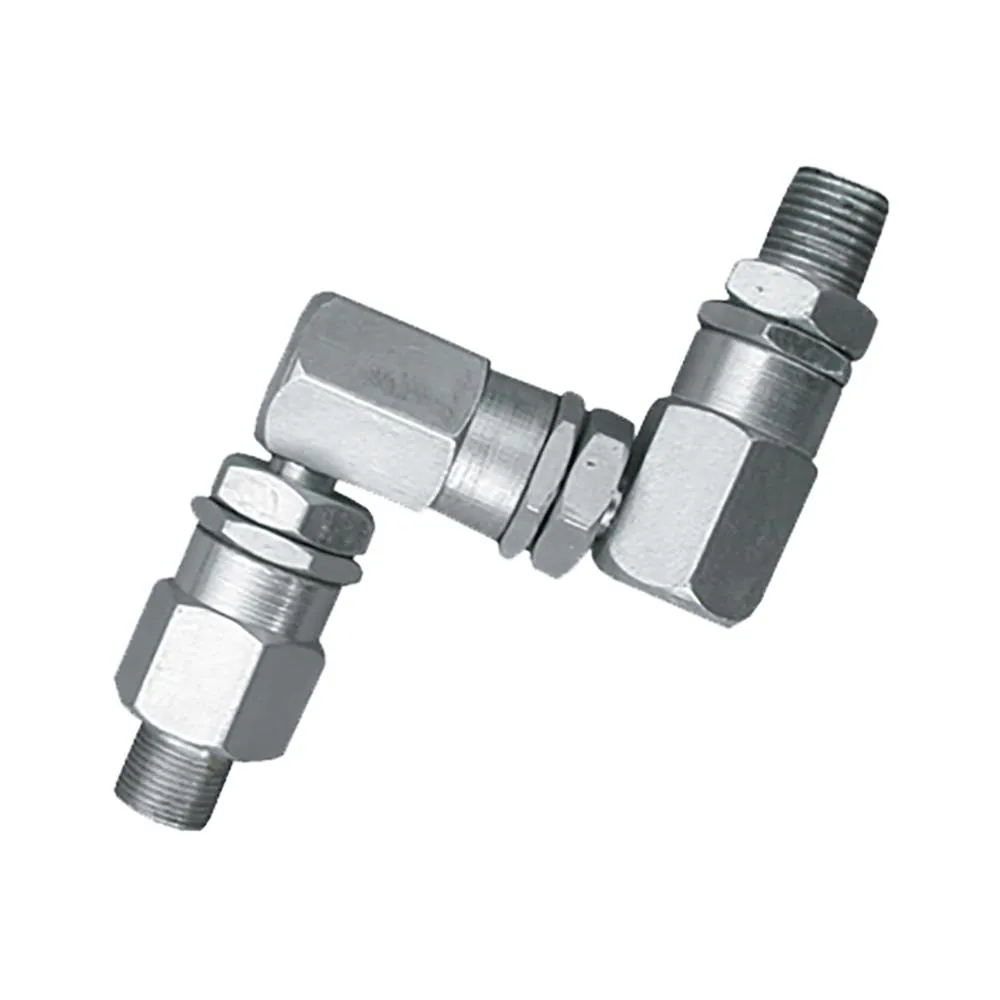
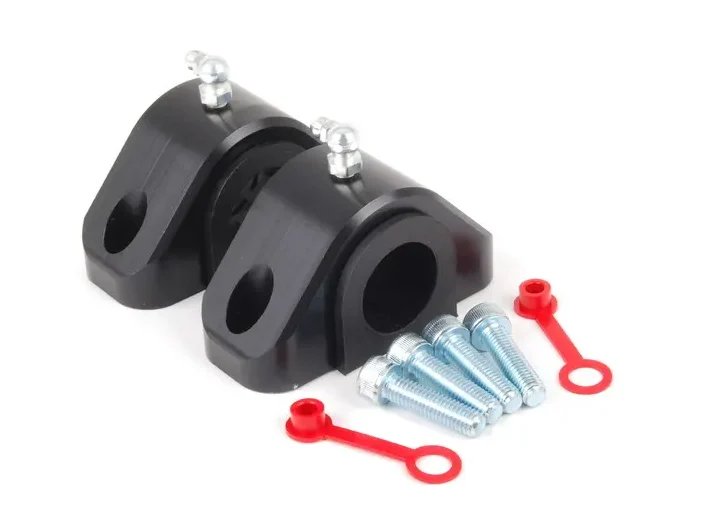
How to Use a Grease Fitting Thread Tester
Grease fitting thread tester quickly identifies fitting thread patterns for every common standard, metric, and British thread grease fitting. Thread pitches include NPT, Metric, UNF, BSW, BSF, and BSPT. Made from high-strength aircraft-grade aluminum alloy.Thread the fitting your trying to identify into one of the holes on the tool that looks correct to the eye.If the fitting will not thread in correctly try the next hole size up or down until the correct fit is found.Each thread size and type are etched on the grease fitting thread tool.
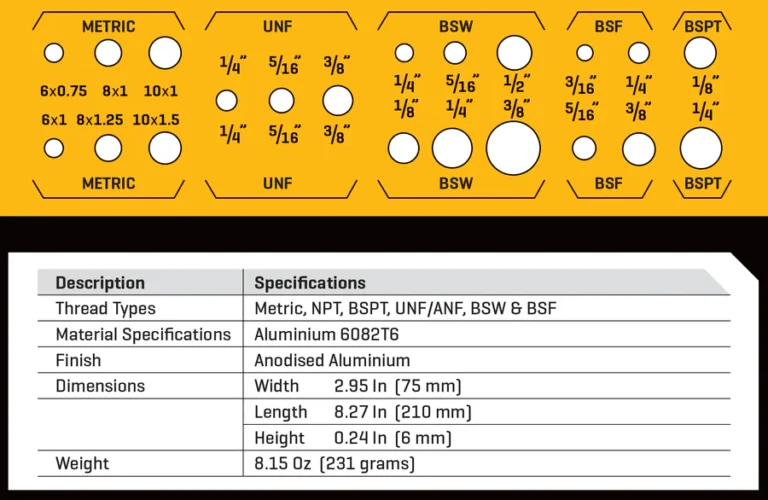
Conclusion
Choosing the right grease fittings type is an essential aspect of proper equipment maintenance, as it ensures effective lubrication that caters to your machinery’s specific needs.
By familiarizing yourself with the different types of grease fittings, their uses, and applications, you’ll be better equipped to make the right decision when selecting a fitting for your particular requirements.
Furthermore, proper handling of a grease gun for precise application, combined with the use of extension hoses and adapters to deliver grease and reach difficult spots, ultimately leads to smoother operations, increased efficiency, and extended equipment life.