A grease gun is a common workshop and garage tool used for lubrications. The purpose of the grease gun is to apply lubricant through an aperture to a specific point, usually from a grease cartridge to a grease fitting or ‘nipple’. The channels behind the grease nipple lead to where the lubrication is needed. The aperture may be of a type that fits closely with a receiving aperture on any number of mechanical devices. The close fitting of the apertures ensures that lubricant is applied only where needed.It is used on daily basis in everyday places, but it is very important in the machine industry, agriculture,…For your machines to work normally and smoothly, regular and proper lubrication is necessary.So lets find everything about grease guns,their anatomy,applications,problems,parts,…
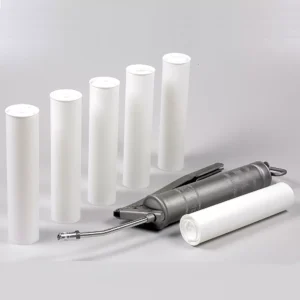
Types of grease gun
Grease guns have three ways in which they can be powered: by hand, air or electricity. Aside from these variations, the hand-powered (or manual) grease guns can either be manufactured with a lever or a pistol grip. The benefits to each of these depend primarily on the intended application and the lubrication technician’s personal preference. One other major variation to the grease gun is how the grease is to be loaded: by suction fill, cartridge or bulk.
Manual (Lever) Grease gun– This is the most common type of grease gun and can supply around 1.28 grams of grease per pump, which is forced through an aperture from hand pumps.
Pros:
- Most common and widely used type of grease gun.
- Relatively simple to use.
- Provides a higher grease output per pump compared to some other manual types.
- No need for external power sources.
- Cons:
- Requires significant hand effort for continuous pumping.
- Might not be as ergonomic for prolonged use.
- The grease output might be a bit messy and less controlled.Grease
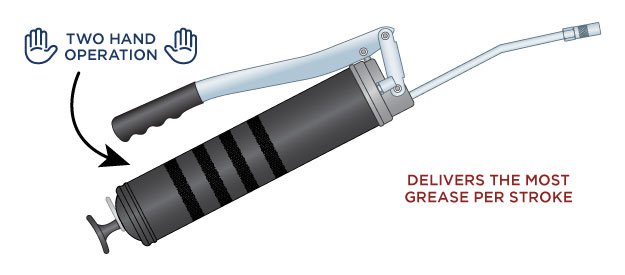
Manual (Pistol Grip) Grease gun– This variation of the lever-type grease gun allows for the one-handed pumping method, which is very common. It provides approximately 0.86 grams per pump.
Pros:
- Allows for one-handed operation, offering more convenience.
- Easier to handle than lever-type grease guns.
- Offers moderate grease output per pump.
- Better control and precision in grease application compared to some other manual types.
- Cons:
- Still requires manual effort for pumping.
- Might not provide as much grease per pump as the lever-type
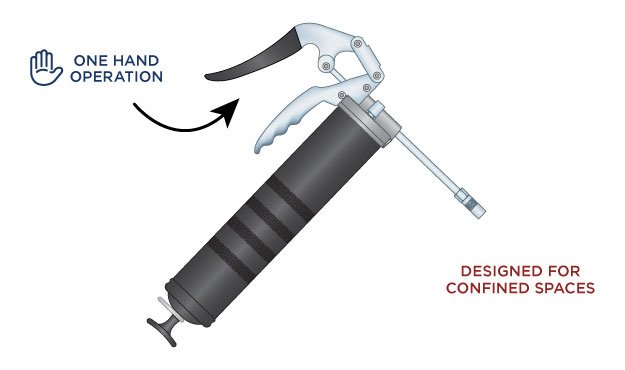
Pneumatic (Pistol Grip) Grease gun– This grease gun uses compressed air directed into the gun by a hose activating a positive displacement with each trigger. Russell Gray, inventor of the air-powered grease gun, founded Graco based on this invention.
Pros:
- Powered by compressed air, which reduces manual effort significantly.
- Offers high-pressure grease output, making it efficient for heavy-duty applications.
- Faster and more efficient than manual types.
- Provides consistent grease dispensing.
- Cons:
- Requires an air compressor or another source of compressed air.
- The setup might be more complex.
- Limited mobility due to the air hose connection.
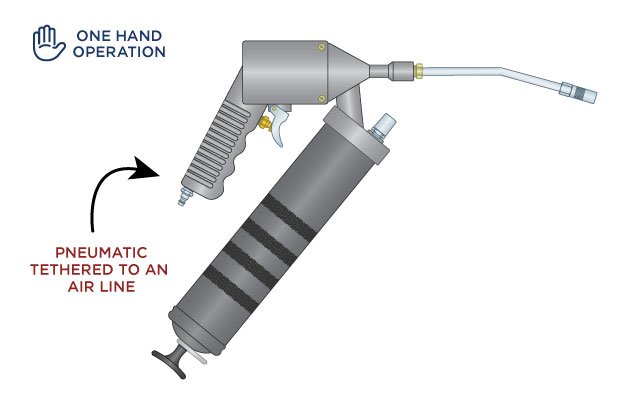
Electric(Pistol Grip) Grease gun – This is a low-voltage, battery-powered grease gun that works comparably to the pneumatic grease gun. It offers the advantage of being cordless.
Sure, here are the pros and cons of each type of grease gun:
Pros:
- Powered by a battery, offering mobility and ease of use.
- Comparable performance to pneumatic grease guns.
- Eliminates the need for an external air compressor.
- One-handed operation for convenience.
- Cons:
- Requires charging or battery replacement.
- Might not offer the same pressure as pneumatic grease guns.
- Higher initial cost due to the battery-powered mechanism.
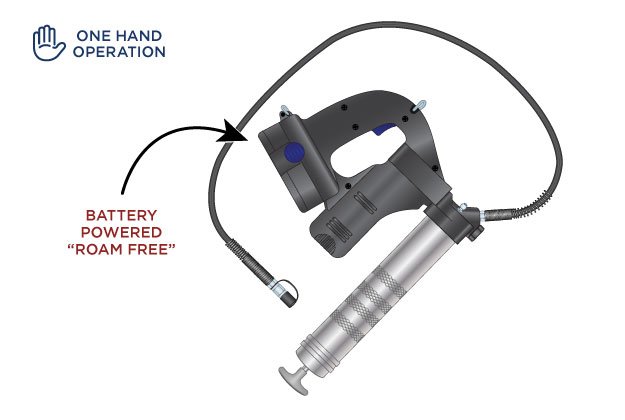
Connectors, Adapters and Couplers
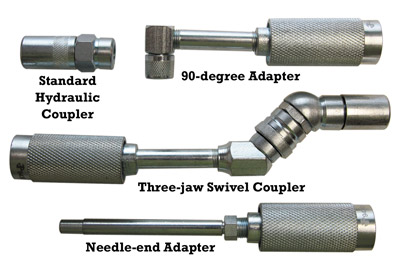
Accessories
Grease gun meters can be retrofitted onto a grease gun to help optimize lubricant consumption. Plastic caps provide benefits such as preventing corrosion and debris. They also can be color-coded so that cross-contamination does not occur. Other accessories such as sonic/ultrasonic devices are also available.

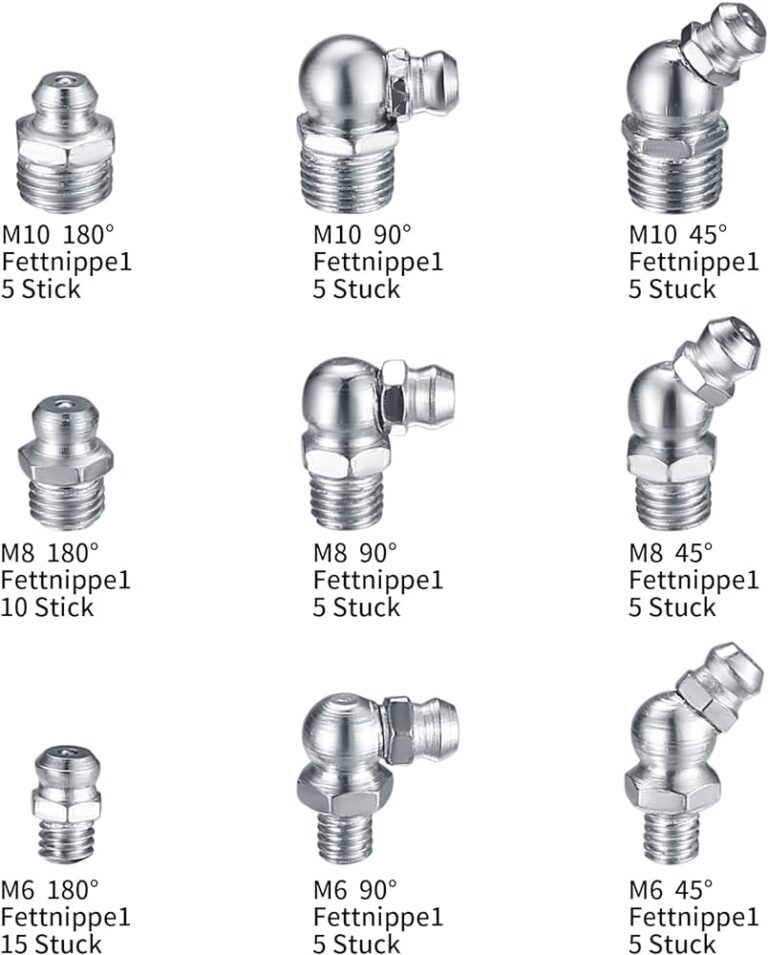
A grease gun may come with the standard connection adapter such as a hydraulic coupler, but there are several variations depending on the application. The standard hydraulic coupler is the most commonly used and most applicable. A 90-degree adapter is ideal for fittings in confined areas that require a 90-degree bend. A needle-end adapter provides a thin, precise amount of grease for tight places, while a three-jaw swivel coupler offers a variety of locking positions for different applications.
Fixed Tube vs. Flexible Hose
The decision to use a flexible hose or a fixed tube depends on the machine’s grease-fitting type and ease of location, as well as the type of grease gun used. For example, a hard-to-reach location would benefit from a flexible tube. On the other hand, lever-style grease guns require both hands to pump the grease and would favor the fixed-tube alternative.

Grease Fittings
grease fittings or a Zerk fitting, grease nipple, or Alemite fitting. This is the lubrication point where the grease connector is attached. The standard hydraulic grease fitting is most commonly used for standard applications. It can be either upright or angled(45,180 or 90°).
The button-head fitting is ideal for good coupler engagement when large volumes of grease are being added. A flush-type grease fitting is preferred when space is limited for standard protruding fittings, while the pressure-relief vent fitting helps prevent higher pressures that could lead to damaged seals.
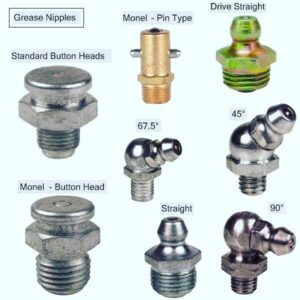
Machine condition Risks Associated with Grease Guns
Not knowing how to precisely measure greasing can lead to damaged seals, fluid friction, and unwanted consumption.
Proceeding with caution can help you protect your machinery and avoid making mistakes. If you find yourself in any doubt about the capability of your grease gun to fix a problem, be sure to consult with some professional in this “area”.
High Grease Gun Pressure
A high-pressure manual grease gun is designed to deliver from 2,000 to 15,000 psi. Applying too much pressure while greasing will damage the bearing seals, which rarely handle more than 500 psi. Symptoms of high grease gun pressure include collapsed bearing shields, damaged bearing seals, grease driven into electric motor windings, and safety and environmental issues.
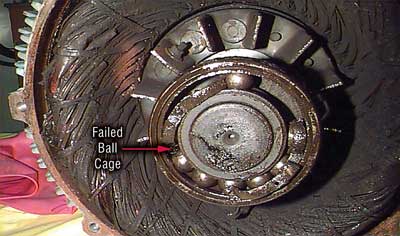
Regreasing Frequency
Managing regreasing frequencies to optimal conditions is necessary to avoid long-term machine health problems. If the frequency is too long, symptoms may include lubricant starvation, which promotes wear, friction, and grease contamination. If the frequency is too short, excessive grease consumption and safety and environmental issues may occur.
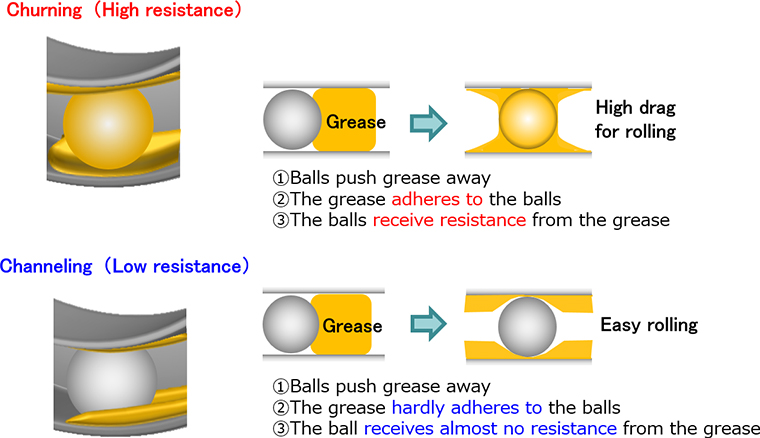
Overgreasing and Undergreasing
It is important to know the exact amount of grease necessary for your greasing application to avoid over-greasing or under greasing. Symptoms of over greasing include damaged seals and motor windings, environmental issues, and fluid friction, which leads to increased heat generation, higher grease oxidation rates, and higher energy consumption. Symptoms of undergreasing include bearing starvation, which results in friction wear and increased contamination.
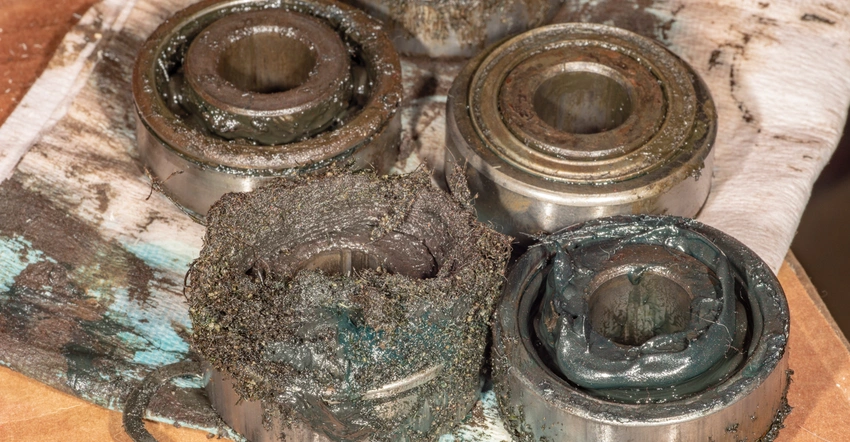
Grease Gun Best Practices
Calculate the proper amount of grease needed for the relubrication of bearings based upon the calibrated delivery volume of the selected grease gun.
Use a vent plug on the relief port of the bearing to help flush old grease and reduce the risk of too much pressure on the bearing.
Use extreme caution when loading grease into the grease gun to ensure that contaminants are not introduced. If using a cartridge, be careful when removing the metal lid so that no metal slivers are introduced into the grease.
Make sure the grease gun is clearly marked to identify the grease with which it should be charged. Do not use any type of grease other than that which is identified.
Always make sure the dispensing nozzle of the grease gun is clean before using. Pump a small amount of grease out of the dispensing nozzle and then wipe the nozzle off with a clean rag or lint-free cloth before attaching it to the grease fitting.
Clean the grease fitting of all dirt before attaching the grease gun. Inspect and replace damaged fittings. It is helpful to use grease-fitting caps to keep them clean, but still wipe fittings clean before applying grease.
Ensure that the proper grease is used at every grease point. Applying the wrong grease can cause an incompatibility problem, which can quickly cause bearing failure. Lubrication points should be clearly identified as to which grease is to be used. This can be done with colored labels, adhesive dots or paint markers.
Grease guns should be stored unpressurized in a clean, cool and dry area and in a horizontal position to help keep the oil from bleeding out of the grease. Grease gun clamps make storage easy and organized. Also, cover the coupler to keep it free from dirt and contaminants.
Calibrate grease guns regularly to ensure the proper delivery volume.
Anatomy of a Grease Gun
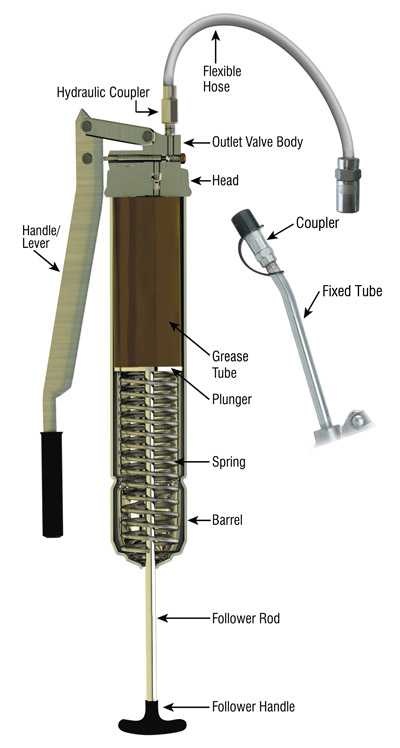
The lever is used in manual configurations of the grease gun for hand-pumping the grease from the barrel to the hose or tube.
The trigger and handle are used in manual configurations of the grease gun for hand-pumping the grease from the barrel to the hose or tube in a similar way as the lever.
The barrel is the exoskeleton of the grease gun that houses either the grease tube or the grease supplied from bulk storage.
The grease tube (or cartridge) is an inserted housing of grease that is replaceable when grease is depleted.
The hydraulic coupler (or connector) is the connection point that holds the hose or fixed tube attached to the head of the grease gun.
The head of the grease gun contains grease pathways and valves that allow the pumping of grease to travel from the barrel into the flexible hose or fixed tube.
The filler nipple is the injection point for grease from a filler pump.
The air-release nipple allows air to escape after new grease has been added to the grease gun and pumped into the head.
The spring provides the pressure onto the plunger.
The follower rod (piston rod, barrel rod, plunger rod) helps the plunger follow a uniform path as it keeps pressure on the bottom end of the grease tube. It also acts in pulling back the spring prior to inserting a new grease tube.
The follower handle offers a grip when pulling the follower rod prior to inserting a new grease tube.
The plunger provides uniform pressure to the back end of the grease tube as grease is depleted.
The flexible hose is used interchangeably with a fixed tube for flexible positioning of the connector or coupler.
How Can I Improve My Grease Gun?
There are some key components to upgrading a grease gun that allow you greater use. These options or upgrades can make it easier to grease driveshafts, PTO shafts, wheel bearings, and hard to reach fittings. Locking couplers ensure you don’t have to hold onto the coupler.These parts include different types of couplers such as:
- safeLOCK locking grease coupler
- 90-degree couplers
- driveshaft couplers
- longer hose
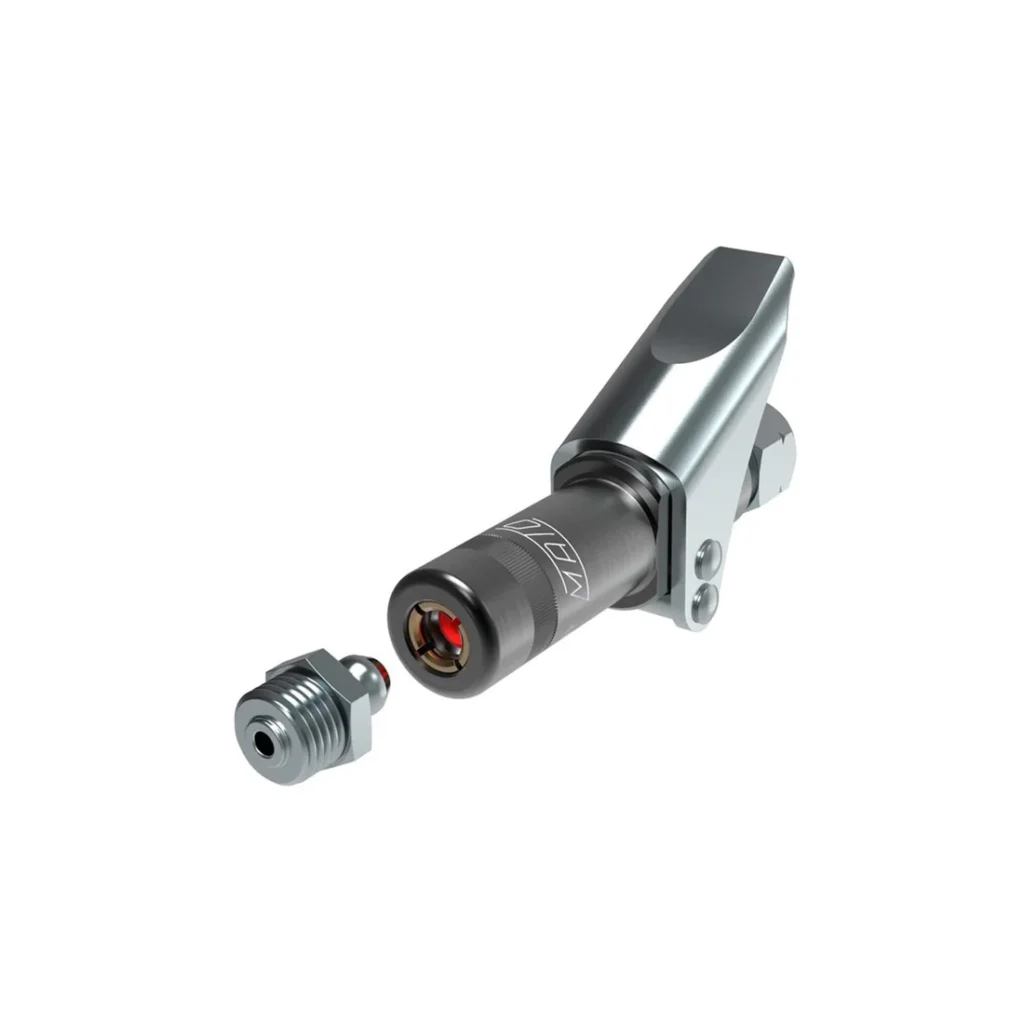
How to a load grease gun
Most grease guns operate on the same principle mechanisms and they are:
- Pull the plunger back (there is a spring inside being compressed when you do this—this is important to know later; more on it below) and rest it on the catch in the tool body.
- Unscrew body from the head.
- If the gun has an old grease tube in it, remove the tube. If the tube is jammed carefully and slowly release the plunger to push the tube out. Re-latch the plunger once you can get a grip on the tube.
- Check that the gasket that seals the tool body to the actuator head hasn’t gotten buried in grease and thrown away with the old tube.
- On the new tube, remove the plastic cap and insert the tube into the tool—open end toward the plunger.
- Remove the pop-top or foil. This lid is astonishingly sharp, be mindful.
- Re-assemble the tool.
- For tools with no bleeder valve, the unit must be primed, or burped, to get any air out. Thread the unit back together and back it off one turn. Release the plunger. You may actually have to push it down through the grease. Tighten the tool and dispense grease onto a piece of cardboard until it flows burp-free. If the handle doesn’t resist the pressure you put on it, there is air in the tool. Keep pumping until the flow is uninterrupted.
- For units with bleeder valves, the air can be evacuated through the valve