Agriculture is among the industries where work greatly affects equipment like tractors, combines, harrows, corn pickers, plows, ballers, seeders, and other machinery. Those who work in the agricultural sector rely on their machines to make their business and fields flourish. No matter the conditions like high humidity, dust, extreme temperature, and heavy usage, each piece has to be reliable and function optimally.
Tractors are the unsung heroes of agriculture, enabling farmers to till vast expanses of land and perform a myriad of tasks essential to food production. Yet, behind their robust exteriors lies a critical component often overlooked but vital for their smooth functioning – Tractor grease. This lubricant plays a main role in ensuring the efficiency, durability, and longevity of these powerful machines and equipment.
Tractor maintenance requires the application of lubricating solutions that can help agricultural professionals overcome daily challenges. Choosing the right tractor grease, oil, and other lubricating fluids specially designed for agricultural machines has the power to boost productivity. How? By providing adequate lubrication, tractors, and other machinery perform to their full potential. Here is what you should pay attention to while choosing the right grease and oil for your tractor.
Tractor grease
Heavy-duty tractor grease performs a number of functions the most important one being lubrication of tractor parts. Adequate lubrication extends the service life of any machine and increases its performance as itreduces friction and heat. In addition, tractor greases are sealants that prevent contaminants from penetrating tractor components. As a result, premature component failure is prevented as wear and tear are minimized. A high-quality grease has the capacity to endure heavy loads and high temperatures, meaning there is no occurrence of oil bleeding when conditions toughen. Also, grease serves as a corrosion protectant because it adheres to metal surfaces and stops moisture from creating problems.
There are many different grease types and knowing the basics helps us to make the right choice. All greases consist of base oil, thickener, and additives.
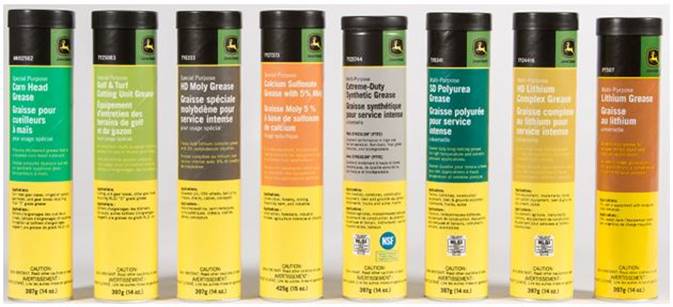
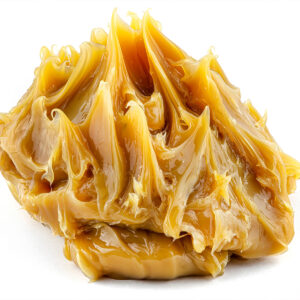
Base oil
The base oil serves as the primary lubricating agent, reducing friction between moving parts. Ranging from mineral oils to synthetics, the choice of base oil depends on factors such as operating temperatures, load-bearing capacity, and environmental conditions.
Mineral greases or conventional greases are said to be most commonly used in agricultural operations due to their price. Synthetic greases, on the other hand, are more expensive alternatives. When we look at their advantages regarding performance, protection, and maintenance intervals, this price difference melts in the long-run.
The choice between mineral or synthetic grease should be made based on the operating conditions. These include temperature (high and/or low), pressure, and load. Simply put, synthetic oils perform better in a range of different temperatures, while mineral greases are a good choice in more constant conditions.
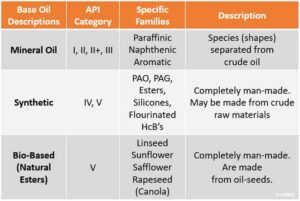
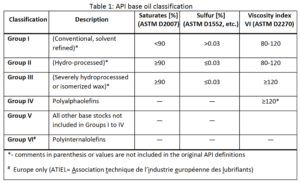
Thickener
Thickeners or thickening agent are there to enable better bonding of grease components (base oil and additives). Thickeners are simple and complex soaps based on lithium, calcium, aluminum, sodium, barium, or other compounds. There are also non-soap thickeners based on clay and polyurea. We differ in a couple of different types of grease :
Lithium tractor grease
A durable and stable multipurpose grease with high viscosity suitable for extreme temperatures, high pressures, and shock loads. It protects equipment against oxidation, corrosion, wear and tear.
Calcium tractor grease
Another multipurpose grease with great water resistance and corrosion protection properties and high mechanical stability. They are used in agriculture when temperatures are lower.
Aluminium complex grease
For high-temperature applications, with water resistance, rust, corrosion, and oxidation prevention properties. Most commonly used in the food industry and farming.
Barium complex grease
High-performance grease for demanding and heavy-load applications (industry, marine, manufacturing, aeronautical). Mechanically stable, resistant to high temperatures, water, oxidation, chemicals, endures heavy loads and high speeds.
Bentone or Clay tractor grease
Lubricant with superior temperature change resistance, great wear and tear protection, exceptional water tolerance, good mechanical or shear stability, and impressive adhesiveness. Often called non-melt lubricant, used in the steel, manufacturing, construction, mining, and ceramic industry.
Polyruea (multipurpose ) tractor grease
Used across various industries due to its properties such as durability, water resistance, oxidation stability, rust and corrosion resistance, high-temperature performance. Typical applications in steel plants and electric motors
Sodium tractor grease
Grease with excellent rust protection, solid sheer stability, and good lubrication. However, it has poor water and oxidation resistance. Typically mixed with other greases for better performance.
A very important note is that the thickener type has to be compatible with the tractor manufacturer’s recommendations and endure the operating conditions. Furthermore, thickeners are not compatible and should not be mixed because they can break down and affect the performance of the lubricating systems.
Additives
To enhance performance and safeguard against corrosion, oxidation, and contamination, manufacturers incorporate additives into the grease formulation. These additives can include anti-wear agents, rust inhibitors, and antioxidants, augmenting the grease’s protective capabilities. The load and pressure also affect the choice of additive package used in the formulation of the grease. Different types of additives enhance grease protective properties such as handling extreme pressure, anti-wear, anti-friction, anti-rust, anti-corrosion, and oxidation inhibition. One common additive for tractors and farm equipment is molybdenum disulfide or moly grease (e.g. Valvoline Multipurpose Moly 2 grease).
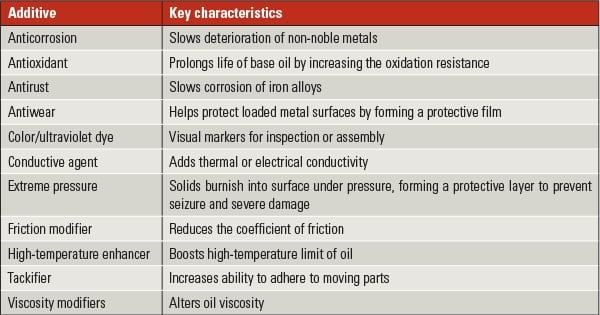
Different types of additives
industrial lubricating oils are made of base oil, which is either mineral or synthetic, and additives. These advanced additives overcome the shortcomings of mineral and synthetic base oils. Depending on the issue they safeguard the oil and lubricated machine against, additives can be divided into several types.
Anti-wear additives
These additives form a protective fluid film on the surface which defends the surface against premature wear and oxidation. Moreover, they are added to oils meant for application at extreme temperatures.
Friction modifiers
They are used for engine oils, in particular, to reduce friction and reduce energy consumption.
Extreme pressure additives
These additives form a very thick and strong protective film. The lubricating oils and industrial grease that contain extreme pressure agents are the ones used for gears lubrication for example. However, their composition causes corrosion to certain materials.
Viscosity index improvers
The application of these additives increases the stability of the oil at a range of temperatures.
Pour point depressants
Their function is to lower the pour point of oil and improve its flowability at low temperatures.
Oxidation inhibitors
These protective agents are added to oils to preserve their lubricating properties as they are exposed to extreme operating conditions (high temperature and pressure) and air.
Detergents and dispersants
These agents clean the surfaces of targeted compounds by reducing the presence of acid and guarding them against rust and corrosion. This is achieved by dispersing any type of contaminants in the oil which prevents the formation of sludge and deposits on metal surfaces even after a period of inactivity
Foam inhibitors
Anti-foaming agents are needed because when different additives interact with each other, they can create foam. Foam can seriously hinder the performance of industrial oil because its air bubbles prevent the oil from lubricating the surface adequately. Interestingly, an inadequate amount of foam inhibitors can have a reverse effect meaning that more foam can occur affecting the oil even more.
It is important to say that all of these additives and their functions weaken with time which also means that the oil itself loses its quality. Once this occurs or the oil’s service life expires, it is time to change the industrial oil.
Grease consistency grades
Greases differ depending on their consistency defined by the National Lubricating Grease Institute (NLGI). NLGI describes the various grease grades primarily based on viscosity and, specifically, working penetration testing. This testing involves a rather elaborate machine that tests the reaction of grease penetration of a known weighted cone-shaped device (it’s sort of like your pocket and a politician – the deeper your pocket, the deeper the politician digs). The levels of grease softness or hardness go from NLGI 000 to NLGI 6, with NLGI 000 being completely fluid to NLGI 6 defined as very hard. Furthermore, the same type of grease cannot be used for all tractor parts. For instance, if your machine has an auto lube system, NLGI 0 or lighter grease is appropriate. When temperatures get higher in the summer, NLGI 2 is recommended. On the other hand, when temperatures drop in winter, NLGI 1 or synthetic grease will enable the equipment to function optimally.
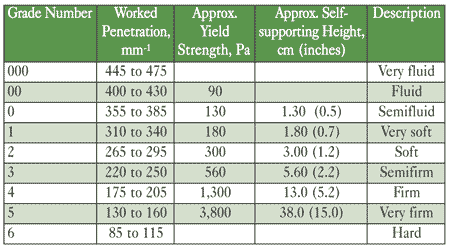
Tractor grease gun
Grease guns are essential to apply heavy lubricants on machinery.
A grease gun is a common workshop and garage tool used for lubrications. The purpose of the grease gun is to apply lubricant through an aperture to a specific point, usually from a grease cartridge to a grease fitting or ‘nipple’. The channels behind the grease nipple lead to where the lubrication is needed. The aperture may be of a type that fits closely with a receiving aperture on any number of mechanical devices. The close fitting of the apertures ensures that lubricant is applied only where needed. There are four types of grease gun:
- Hand-powered,lever handle grease gun where the grease is forced from the aperture by back-pressure built up by hand-cranking the trigger mechanism of the gun, which applies pressure to a spring mechanism behind the lubricant, thus forcing grease through the aperture.Lever guns require two hands to operate.
- Pistol-grip grease gun, where there is no trigger mechanism, and the grease is forced through the aperture by the back-pressure built up by pushing on the butt of the grease gun, which slides a piston through the body of the tool, pumping grease out of the aperture. Pistol grip guns typically dispense less grease per stroke than a standard two-handed lever gun.
- Pneumatic grease gun , where compressed air is directed to the gun by hoses, the air pressure serving to force the grease through the aperture. Russell Gray, inventor of the air-powered grease gun, founded Graco based on this invention.
- Electric, Cordless Grease Guns, where an electric motor drives a high-pressure grease pump. These are often battery-powered for portability. Cordless grease guns are trigger operated, portable, and convenient.
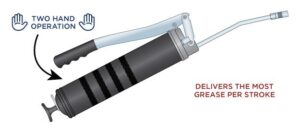
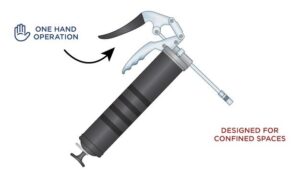
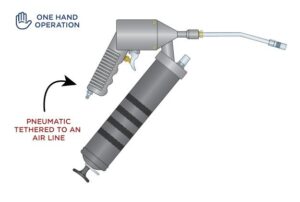
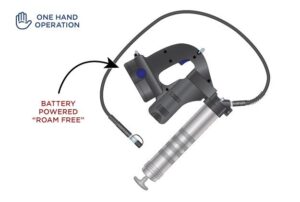
What are greas gun used for?
Grease guns are used to lubricate a wide variety of parts on a vehicle’s chassis and running gear. Prior to the 1980s, “chassis lubrication” was a standard part of most automotive service visits, but as more components like bushings, kingpins and bearings became sealed-for-life, less attention needed to be paid. Grease guns are used to inject components such as wheel bearings, universal joints, steering joints, and more, with the lubricants needed to keep them moving freely and prevent parts from wearing out.
Conclusion
Tractor maintenance might at times be a time-consuming process. Nevertheless, when adequate lubrication is provided, the tractor service intervals are lowered increasing overall efficiency. Choosing the right tractor grease, oil for tractors, and other lubricants always has to be done in accordance with the equipment manufacturer’s recommendations. They have to be lubricants engineered for heavy-duty applications such as agriculture. In addition, operating conditions also play an important role in the selection of lubricants.
Pingback: Best Grease Gun : Tips and tricks - Ekvux